iron ore pellet process
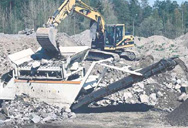
Iron Ore Pelletizing Process: An Overview - ResearchGate
2018年7月11日 The iron ore pellet holds a pivotal role in the ironmaking process, enabling the utilization of high-grade ore and the upgrading of low
More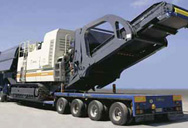
Iron Ore Pelletization: Part I. Fundamentals: Mineral Processing
2021年3月15日 Iron ore concentration typically involves comminution, separation, and agglomeration. Comminution is the grinding of the ore to liberate the valuable iron-bearing
More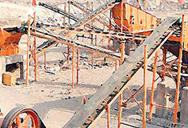
Iron ore pelletization - ScienceDirect
2015年1月1日 A brief introduction to recent developments in iron ore pelletizing is provided in this chapter, including the world output of fired pellets, pellet production processes,
More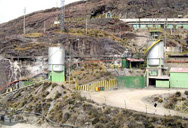
(PDF) Iron ore pelletization - ResearchGate
2015年12月31日 A brief introduction to recent developments in iron ore pelletizing is provided in this chapter, including the world output of fired pellets, pellet production processes, preparation of...
More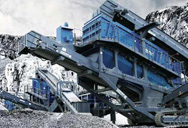
Iron Ore Pelletization: A Critical Review of Processes and ...
Iron ore pelletization is a central process in the steel industry, transforming iron ore fines into pellets that can be efficiently smelted in blast furnaces. As high-grade natural iron ore
More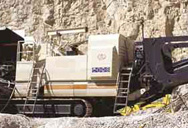
Iron Ore Pelletizing Process: An Overview - Semantic
2018年7月11日 However, the content of iron in ore deposits has deteriorated and low-grade iron ore has been processed. The fines resulting from the concentration process must be agglomerated for use in iron and
More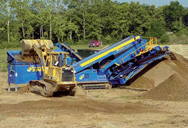
A new insight into iron ore oxidized pellets prepared by steel belt ...
2024年9月14日 Iron ore oxidized pellet is a superior furnace burden for the blast furnace process, possessing high iron grades, good strength, and excellent metallurgical properties [1].
More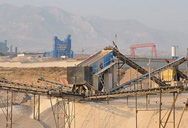
(PDF) IRON ORE PELLETIZING PROCESS - ResearchGate
2023年11月15日 IRON ORE PELLETIZING PROCESS. November 2023. DOI: 10.13140/RG.2.2.16218.11204. Conference: Department of Geology, Tanta University. Authors: Hassan Z. Harraz. Tanta...
More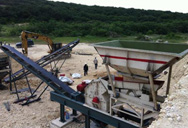
A New Approach of Pelletizing: Use of Low-Grade Ore as a
2024年9月10日 The pelletizing process mostly uses high-grade iron ore such as magnetite (Fe 3 O 4) as the main raw material, which has been depleted due to the increasing demand for
More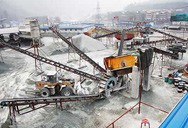
Iron Ore Pellets and Pelletization Process - IspatGuru
2014年11月26日 Iron Ore Pellets and Pelletization Process. Pelletizing of iron ore was started in the 1950s to facilitate the utilization of finely ground iron ore concentrates in steel production. For the pelletizing of iron ore there are two main types of processes namely, the straight travelling grate (STG) process and the grate kiln (GK) process.
More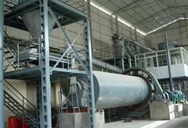
What is Iron Ore Pelletizing? How It Worked? An In-depth Look at
Iron ore pelletizing is an essential industrial process that transforms powdery iron ore into uniform, robust pellets, serving as a premium feedstock for blast furnaces and direct reduction reactors. This process has witnessed significant advancements since its inception, primarily driven by the escalating requirements of the steel industry, which demands higher quality and
More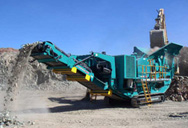
Iron Ore Pelletizing Process: An Overview
2018年7月11日 The iron ore production has significantly expanded in recent years, owing to increasing steel demands in developing countries. However, the content of iron in ore deposits has deteriorated and low-grade iron ore has
More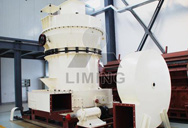
(PDF) IRON ORE PELLETIZING PROCESS - ResearchGate
2023年11月15日 Iron Ore, Iron Ore Pellets, Direct Reduced Iron )DRI( Pellets, Iron Ore Pellets Market, Pelletizing Process, Sintering, Binder, Induration Technology, Straight Grate, Grate-Rotary kiln The iron ...
More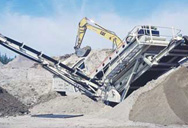
Iron Ore Pellet - an overview ScienceDirect Topics
The Direct Reduction of Iron. Thomas Battle, ... James McClelland, in Treatise on Process Metallurgy: Industrial Processes, 2014. 1.2.2.2 Agglomeration of Iron Ore. The three major forms of iron used in ironmaking are pellets, lump, and sinter. The major change in the past 50 years has been the development of cost-effective pelletization technology allowing pellets to be a
More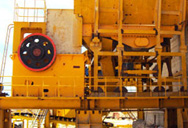
Iron Ore Pelletization: A Critical Review of Processes and ...
Iron ore pelletization is a critical aspect of the steel manufacturing process, providing a method to utilize fine iron ore particles and beneficiate lower grade ores, which enhances the overall output and efficiency of steel production processes. Pelletization involves converting iron ore fines into compact pellets, which are then used in blast furnaces or direct reduction iron
More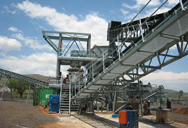
Utilization of High-Alumina Iron Ore in Pellet Making Through Process
2024年7月3日 The demand for pellets in blast furnaces has recently increased because of their uniform shape and size, controlled chemistry, iron-enriched feed, high strength, and quality consistency. To meet this demand, low- and medium-grade iron ore fines with alumina (> 3.5 wt%) must be used for pelletization because of the limited availability of high-grade ore. The
More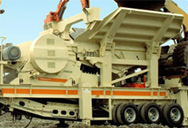
What Are Iron Ore Pellets and How to Make Them?
2023年5月29日 They contain 64-72% iron and additional materials, which can adjust the chemical composition and metallurgical properties of the pellets. The iron ore pelletization is the process of converting iron fines less than 200 mesh (0.074 mm) into 8-16 mm pellets. Types of iron ore pellets Iron ore pellets are normally produced in two types of quality ...
More
Mechanism of thermal compressive strength evolution of carbon
2024年5月27日 Against the background of “carbon peak and carbon neutrality,” it is of great practical significance to develop non-blast furnace ironmaking technology for the sustainable development of steel industry. Carbon-bearing iron ore pellet is an innovative burden of direct reduction ironmaking due to its excellent self-reducing property, and the thermal strength of
More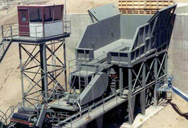
Mechanism of magnetite iron ore concentrate morphology
2022年12月1日 1. Introduction. Iron ore pellets are one of the significant sources of iron for iron and steel making due to their superior metallurgical performance, low energy consumption, and less emission of environmentally harmful dust and gases during the production process [1], [2], [3].The two primary raw materials for pellet production are hematite and magnetite
More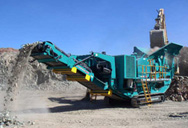
Cooling Air Velocity on Iron Ore Pellet Performance Based on
2024年8月14日 During the pellet cooling process, cooling air velocity is crucial for optimizing the cooling rate, evaluating the utilization rate of cooling heat energy, and improving pellet performance. As the simulated cooling air velocity increased, the gas temperature at the cooling endpoint decreased from 87 °C to 51 °C, and the solid temperature decreased from 149 °C to
More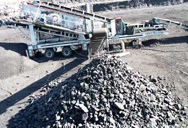
Porosity of Iron-Ore Pellets at Different Stages of Roasting and ...
2024年3月21日 Abstract Metallurgical properties are determined by the structure of pellets at the macrolevel as well as at the level of minerals and elements. The goal of this work is to analyze changes in the porosity of iron-ore pellets during their lifecycle, from pelletizer to full reduced state. The model used in this work relies on several assumptions: (1) the primary porosity of
More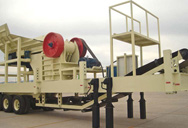
A novel iron ore pelletization for increased strength under
2018年9月1日 This process greatly reduces the energy required to produce the iron ore pellets of high strength. As it is not necessary to heat the pellets up to 1350 °C to achieve similar strength saving on fuel and emissions. In addition, great reduction in CO 2 emission is observed during the iron oxide reduction process.
More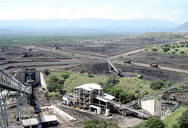
An integrated optimal control model for the drying and
2024年1月12日 Wang Y, Fan X, Chen X. Mathematical models and expert system for grate-kiln process of iron ore oxide pellet production (Part I): mathematical models of grate process. J Central South Univ Technol (Engl Ed) 2012; 19: 1092–1097. Crossref. Google Scholar. 19.
More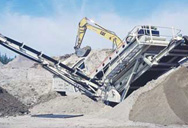
Iron Ore Pellet - an overview ScienceDirect Topics
The Direct Reduction of Iron. Thomas Battle, ... James McClelland, in Treatise on Process Metallurgy: Industrial Processes, 2014. 1.2.2.2 Agglomeration of Iron Ore. The three major forms of iron used in ironmaking are pellets, lump, and sinter. The major change in the past 50 years has been the development of cost-effective pelletization technology allowing pellets to be a
More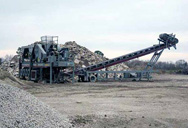
Introduction to Iron ore Pellets and Pelletizing processes
2013年2月23日 Process technology. There are four stages involved in the production of iron ore pellets. These stages consist of (i) raw material preparation, (ii) formation of green balls or pellets, (iii) induration of the pellets, and (iv) cooling, storage and transport of pellets.
More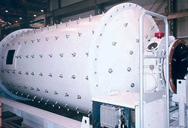
Developing Iron Ore Pellets Using Novel Binders for H
2023年7月23日 The transformation from traditional iron- and steelmaking technologies to green H2-based new technologies will require an improvement in the quality and purity of iron ore burden materials. Iron ore pellets are essential inputs for producing direct reduced iron (DRI), but the conventional binders, used in iron ore pelletizing, introduce gangue oxides to the DRI
More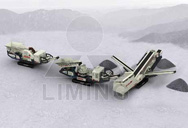
Combustion Evaluation of Renewable Fuels for Iron-Ore Pellet
2019年7月18日 Induration (or sintering) of iron-ore pellets requires high temperature (∼1300 °C), which today is generated by burning fuel oil in the firing zone of the straight-grate plant (SG) or coal in the rotary kiln of grate-kiln (GK) plants. In this study, ∼150 kWth combustion experiments were used to investigate the opportunity of totally replacing fuel oil with H2 or
More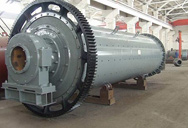
Improving properties of fluxed iron ore pellets with high-silica by ...
2021年9月20日 Iron ore pellets have been proved to possess preferable size and shape, mechanical strength and metallurgical properties, compared with the sinters during the blast furnace ironmaking process [4, 5]. Under the background of green development, it is an inevitable trend to increase the proportion of pellets in blast furnace burden.
More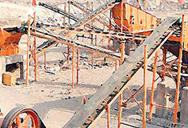
Direct reduction of iron ore pellets by H2-CO mixture: An in-situ ...
2023年8月1日 The impacts of various mixed H 2-CO atmospheres and temperatures (800–1000 ℃) on the reduction swelling of iron ore pellets were studied herein via in-situ infrared imaging of the pellet swelling process and subsequent analysis, which provides theoretical guidance for the development of gas-based shaft furnace technology for low-grade iron ore resources in the
More