Why Limestone Is Used In Clinker Grinding
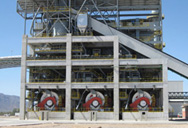
Cement clinker - Wikipedia
Portland cement clinker (abbreviated k in the European norms) is ground to a fine powder and used as the binder in many cement products. A small amount of gypsum (less than 5 wt.%) must be added to avoid the flash setting of the tricalcium aluminate (Ca3Al2O6), the most reactive mineral phase (exothermic hydration reaction) in Portland clinker. It may also be combined with other active ingredients or cement additions to produce other types of cement including, followin
More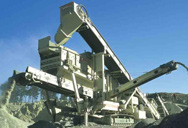
Clinker Grinding Techniques in Cement Manufacturing
2023年10月19日 It can be best described as a nodular material, usually grayish in color, which is produced by sintering limestone and alumino-silicate materials such as clay at high temperatures in a cement kiln. The resulting clinker is
More
Effects and Control of Chemical Composition of Clinker
2020年10月1日 Cement substance is produced by grinding a mixture of a clay and limestone together and heating to a temperature of 1450°C. In which the
More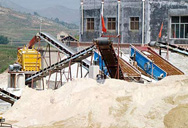
Understanding Limestone in Cement - Concrete Construction
2015年3月26日 The added limestone in the U.S. is modern portland cement and consists of ground clinker, a source of readily soluble sulfates and functional additives. The change is that the specification adds up to 5% limestone. The biggest difference in production is that the limestone is added to the clinker blend before grinding.
More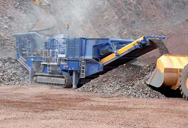
Everything you need to know about clinker/cement
The quantity of grinding aid used in a particular mill is dependent on the size of the mill, feed size, product size, type of clinker being ground, etc. For instance, in large diameter ball mills, the impact force of the grinding media is so great,
More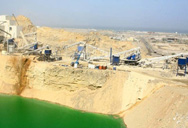
Cement Clinker Calcination in Cement Production
Raw Materials Crushing, Storing and Grinding. Clinker calcination is the most crucial part of the whole process of cement manufacturing. At this stage, ground raw materials will be sent into the cement kiln and be heated at a high
More
Cracking the Code: The Mystery Behind Why Clinker is Hard to
2024年5月14日 Moreover, utilizing specialized grinding techniques, such as pre-grinding or inter-grinding additives, can further enhance the grindability of clinker. Pre-grinding involves crushing the clinker before it enters the mill, while inter-grinding additives are blended with the clinker during the grinding process to reduce particle agglomeration and ...
More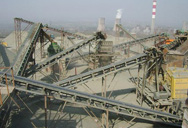
Why Clinker Matters A Look at its Properties and Applications
Versatility: Clinker can be used in various applications, such as soil stabilization, agriculture, and alternative fuel sources, in addition to cement production. Availability: The raw materials used to produce clinker, such as limestone and clay, are abundant and widely available, making it a readily available material. Disadvantages:
More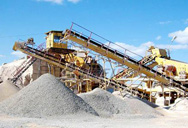
What is Clinker? The Importance of Clinker in Cement Production
To make it clear, more energy is spent when grinding the clinker material with a hard structure compared to grinding the clinker material with a soft structure. ... it is another deferrite. It has 8 percent usage in clinker production. It is a limestone with a dense clay content, which is considered as the source of alumino silicate, ...
More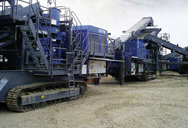
Cement Clinker - an overview ScienceDirect Topics
Report of UNEP SBCI WORKING GROUP ON LOW-CO2 ECO-EFFICIENT CEMENT-BASED MATERIALS. Ellis Gartner, Tongbo Sui, in Cement and Concrete Research, 2018. 1 Introduction. The term “alternative cement clinker ” as used here refers to a man-made mineral material that, when ground to a fine powder, is capable of reacting sufficiently rapidly with water and/or CO 2
More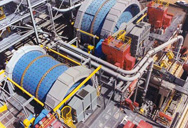
Resistance to Grinding and Cement Paste Performance of Blends
2021年4月19日 Grinding of finished cement is performed in a single stage, intergrinding materials with very different grindabilities. This intergrinding process has many different interactions among the different components of the finished cement. In a context of developing more sustainable and less energy intensive processes, it is important to understand the
More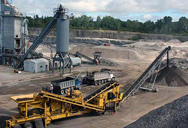
Clinkerization - Cement Plant Optimization
Clinker cooler serves two main objective of cooling clinker from temperature of about 1350 0C to the temperature (65-150 0C) where it can be handled by conveyors like pan conveyors, chain, Elevators etc. and heat recovery from hot clinker coming out of kiln. A huge development has happened in clinker coolers designs and types as well.
More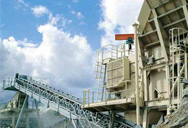
Cement kiln - Wikipedia
Portland cement clinker was first made (in 1825) in a modified form of the traditional static lime kiln. [2] [3] [4] The basic, egg-cup shaped lime kiln was provided with a conical or beehive shaped extension to increase draught and thus obtain the higher temperature needed to make cement clinker.For nearly half a century, this design, and minor modifications, remained the only
More
Cracking the Code: The Mystery Behind Why Clinker is Hard to
2024年5月14日 Moreover, utilizing specialized grinding techniques, such as pre-grinding or inter-grinding additives, can further enhance the grindability of clinker. Pre-grinding involves crushing the clinker before it enters the mill, while inter-grinding additives are blended with the clinker during the grinding process to reduce particle agglomeration and ...
More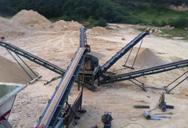
Limestone Addition in Cement Request PDF - ResearchGate
2012年1月1日 Addition of fine limestone provides an excellent means to reduce the amount of clinker in cement. It is now well accepted that limestone partially reacts in cementitious systems with C3A to ...
More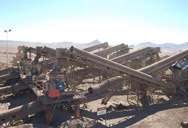
Energy-Efficient Technologies in Cement Grinding
2016年10月5日 Multi-compartment ball mills and air separators have been the main process equipments in clinker grinding circuits in the last 100 years. They are used in grinding of cement raw materials (raw meal) (i.e. limestone,
More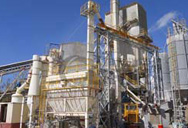
CEMENT RAW MATERIALS
and alumina. Finished cement is produced by finely grinding together around 95% cement clinker with 5% gypsum (or anhydrite) which helps to retard the setting time of the cement. The quality of cement clinker is directly related to the chemistry of the raw materials used. Around 80–90% of raw material for the kiln feed is limestone.
More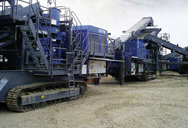
Cement Clinker - an overview ScienceDirect Topics
Report of UNEP SBCI WORKING GROUP ON LOW-CO2 ECO-EFFICIENT CEMENT-BASED MATERIALS. Ellis Gartner, Tongbo Sui, in Cement and Concrete Research, 2018. 1 Introduction. The term “alternative cement clinker ” as used here refers to a man-made mineral material that, when ground to a fine powder, is capable of reacting sufficiently rapidly with water and/or CO 2
More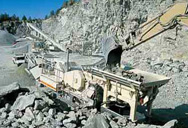
Limestone scenario in India - Indian Cement Review
2020年1月3日 Cement manufacturing process could itself be divided into clinkering and grinding processes, where clinker becomes an intermediate product involving calcination of limestone. Limestone is used in clinkering process by finely grinding it into powder along with admixture of either/or clay, sand, bauxite, iron, etc. is calcined (heated up) at a ...
More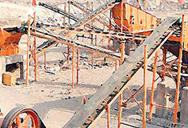
Cement Clinker: Its Types, Uses and Composition
2024年9月16日 Cement clinker is an intermediary product produced during the manufacturing of cement. It looks solid and dark grey in colour. It is collected as lumps or nodules appear in 3mm to 25mm in diameter. The cement clinker is produced by heating clay and limestone together at a temperature range of 1400 to 1500 degrees Celsius.
More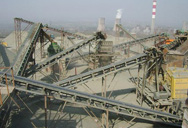
Why Clinker Matters A Look at its Properties and Applications
Versatility: Clinker can be used in various applications, such as soil stabilization, agriculture, and alternative fuel sources, in addition to cement production. Availability: The raw materials used to produce clinker, such as limestone and clay, are abundant and widely available, making it a readily available material. Disadvantages:
More
Better and cheaper cement: Optimising the right clinker properties
2021年5月24日 Large clinker nodules (Figure 2) are difficult to cool, transport and grind into cement. Clinker should ideally have a smaller average nodule size and a narrow nodule size range. More uniformly sized clinker is more evenly distributed into the cooler and has more consistent bed porosity, which enables more stable cooler and kiln operation.
More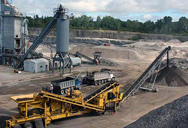
Clinkerization - Cement Plant Optimization
Clinker cooler serves two main objective of cooling clinker from temperature of about 1350 0C to the temperature (65-150 0C) where it can be handled by conveyors like pan conveyors, chain, Elevators etc. and heat recovery from hot clinker coming out of kiln. A huge development has happened in clinker coolers designs and types as well.
More