grinding pressure milling
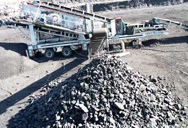
Analysis of hold-up and grinding pressure in a spiral jet mill using ...
Here, the spiral jet mill is studied using a four-way coupled CFD-DEM scheme [20–23] to analyse the effect of grinding pressure and hold-up on particle behaviour and the fluid flow field. The basis for the mill is the Hosokawa Micron AS-50 (Runcorn, UK).
More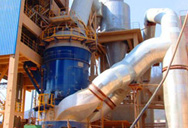
Effect of grinding nozzles pressure on particle and fluid flow
2021年12月1日 Using a four-way coupled DEM-CFD simulation methodology, the particle dynamics and fluid motion in a spiral jet mill (Hosokawa Micron AS-50) were analysed for four
More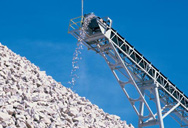
Jet mill working principle
Jet mills operate in compressed air, gas or high pressure superheated steam. Jet mills have no moving parts, thereby eliminating contamination due to contact with external grinding media. It is also an ideal process to grind heat-sensitive and
More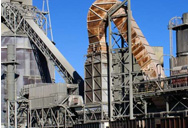
High Pressure Grinding Rolls for Minerals - AusIMM
The characteristics of high pressure grinding rolls are : - energy efficiency - high and steady throughputs - low space requirement, compact design - lower capital operating costs than
More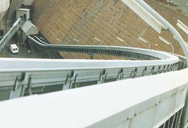
Evaluating the performance of an industrial-scale high pressure ...
2023年1月1日 This paper presents the commercial implementation of a novel comminution circuit with high pressure grinding rolls (HPGR) followed by tower mill in a copper–lead–zinc
More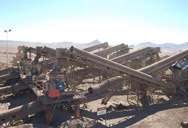
High-pressure mill, High-pressure grinding mill - All
Find your high-pressure mill easily amongst the 16 products from the leading brands (LONGI, Hosokawa, Metso, ...) on DirectIndustry, the industry specialist for your professional purchases.
More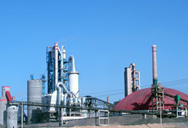
Grinding - Hosokawa Alpine
From pre-crushers for the comminution of coarse materials to jet and ball mills for ultra-fine grinding: Hosokawa Alpine offers mills for a wide range of fineness levels. The mill type that is best suited to your application depends not only
More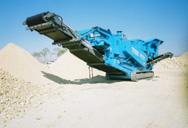
Unifying high-pressure grinding rolls models - ScienceDirect
2022年3月15日 This paper unifies high-pressure grinding rolls crusher (HPGR) models of the working gap, mass flow rate, power draw, and centre and edge product particle size
More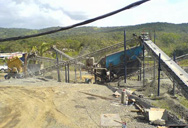
FLS High Pressure Grinding Rolls – Efficient grinding
Optimise your results with a high pressure grinding roll (HPGR), the most energy-efficient way to process mining ores. Suitable for industries including iron ore, precious metals, base metals
More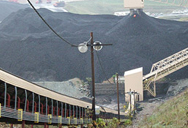
Analysis of hold-up and grinding pressure in a spiral jet mill
2021年6月7日 As a consequence, a better grinding efficiency was expected and also confirmed with decreasing milling nozzle number by grinding experiments, as the new type of experimental apparatus was ...
More
Milling (machining) - Wikipedia
A 3-axis clone of a Bridgeport-style vertical milling machine. Milling is the process of machining using rotary cutters to remove material [1] by advancing a cutter into a workpiece.This may be done by varying directions [2] on one or
More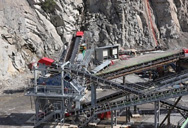
How HPGRs compare to conventional milling Weir
2019年8月19日 Within comminution circuits, High Pressure Grinding Rolls (HPGR) are increasingly replacing conventional SAG, rod and ball mills for hard rock reduction – owing to their substantially lower energy consumption and
More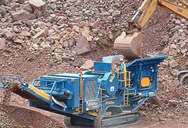
All About Milling in Machining - Xometry
2023年10月24日 Common Milling Methods. Climb and conventional are the two most widely used milling methods in manufacturing. Climb milling (sometimes called “down milling”) rotates the tool against the direction of the workpiece’s motion, so the tool moves in the same direction as the material feed, with the cutter climbing over the workpiece. This method offers smooth
More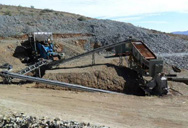
A Review of the Modeling of High Pressure Grinding Rolls
High Pressure Grinding Rolls (HPGR) technology is accepted as an energy-efficient and cost-effective alternative for treating specific mineral ore types. HPGR technology has been advancing within manufacturing facilities and research centers since its first installation in 1985. Over the last three decades much of the literature on HPGR have focused on the industrial applications and
More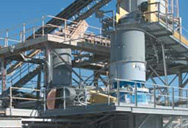
Grinding Mills for reliable size reduction tasks - RETSCH
Cutting grinding is particularly effective for materials that are too tough for impact or pressure grinding but can be efficiently sliced, such as certain plastics, fibrous materials, and foods. The precision of the cut can be adjusted by changing the speed of the cutting blades, their sharpness, and the spacing between them.
More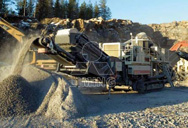
Grinding ABB
On average, milling is the process that requires the most energy in the whole mining operation. To ensure profitable operations, an efficient grinding circuit has to be designed, ... Gearless mills, ring-geared mills and high pressure grinding rolls. Our comprehensive grinding portfolio offers solutions for all your applications.
More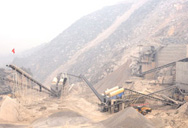
What is Milling?- Definition, Process, and Operations - Mechdaily
Milling covers a wide variety of different operations and machines, from small individual parts to large, heavy-duty group milling operations. It is one of the most widely used processes of machining custom parts with precise tolerances. Milling can be done in different directions on one or more axes, cutting head speed and pressure.
More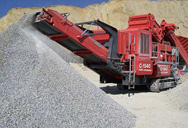
Evaluating high pressure milling for liberation enhancement and
1997年9月1日 Evaluating high premm milling 1015 The specific objeclives of the test programme were to: 1) establish ite level of grind required to achieve substantial liberation as determined by release analysis using a conventional grinding route 2) establish Lhe high compression conditions to achieve a level of liberation equivalent to that achieved by
More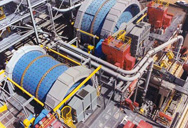
Chapter 8 Air Jet Milling - ScienceDirect
2007年1月1日 The penetration angle of the jet also affects the grinding circle and it is found that the optimum is between 52° and 60°. The injector pressure is fixed higher than the nozzle pressure to avoid back flow but only slightly higher so as to disturb the grinding circle as little as possible. A value of grinding pressure+0.5 bar is often recommended.
More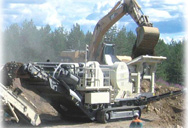
Grinding Mills and Their Types – IspatGuru
2015年4月9日 They are based on attrition grinding between two circular stones, one rotating and the other stationary. Plate mills use a similar principle but are constructed of steel or ceramic plates and used more commonly in the
More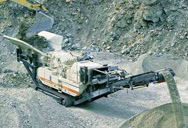
Atmospheric pressure cold plasma jet–assisted micro-milling
2021年1月6日 Here, we propose to induce atmospheric pressure plasma jet to the micro-milling area to improve machinability and surface quality of TC4 titanium alloy. ... Experimental evaluation of the lubrication performance of mixtures of castor oil with other vegetable oils in MQL grinding of nickel-based alloy. J Clean Prod 140:1060–1076.
More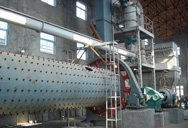
Energy-Efficient Technologies in Cement Grinding
2016年10月5日 Energy-efficient equipments such as high-pressure grinding rolls, vertical roller mills, CKP pre-grinders, Cemex ® mills and Horomills ® are used at both finish grinding of cement and raw material-grinding stages due
More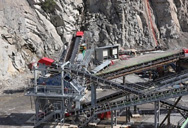
HIGH PRESSURE GRINDING ROLLS—A PROMISING AND COST
High pressure grinding rolls were successfully intro-duced in the cement industry in the late 1980s and enabled appreciable reduction in energy consumption. ... HPGR grinding and ball milling can be 40% lower as against SAG milling, which allows reduction of cost by more than USD 1 per ton for some types of ore.
More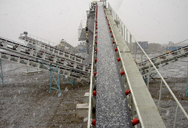
Analysis of grinding in a spiral jet mill. Part 1: Batch grinding
2020年11月1日 Jet milling is widely used in several industrial applications to produce fine particles with a narrow size distribution. We studied by means of experiments, the influence of grinding pressure ...
More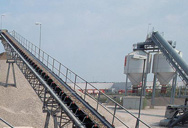
Process optimization and particle engineering of micronized drug ...
2017年11月13日 Critical process parameters of fluid energy mills include grinding pressure, number of grinding nozzles, feed pressure, and feed rate . Media or ball milling can be performed in dry or wet conditions, though wet grinding generally results in a finer product due to the reduction in particle strength and the dispersing effect of the liquid medium [ 27 ].
More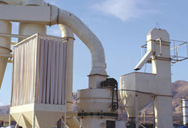
Jet Milling And Particle Classfication - Fluid Energy Processing and ...
Centrifugal, reciprocating, and rotary screw compressors have all been used in jet milling operations, with the latter being the most common. It is recommended that the compressor deliver a minimum of 100 psig to a maximum of 140 psig to the mill. The higher the grinding pressure, the finer the grind.
More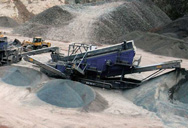
Grinding and Polish – Introduction to Mechanical Design and
The grinding ratio is defined as the ratio of the volume of material removed from the workpiece to the volume of material removed from the wheel. A high grinding ratio means that the wheel wears less and lasts longer. Polishing is a process that uses finer abrasives or polishing compounds to create a smooth and shiny surface on a workpiece.
More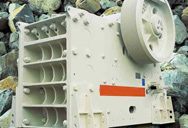
Effect of grinding nozzles pressure on particle and fluid flow
2021年12月1日 The mill has no moving parts, as it is operated using high pressure gas through nozzles, providing fluid energy for grinding and milling. This leads to low maintenance effort and contamination of the final product. The grinding gas nozzles induce an internal vortex and cause interparticle collisions.
More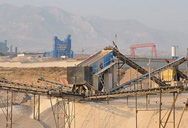
Ultrasonic Wet-Milling and Micro-Grinding - Hielscher Ultrasonics
Ultrasonication is an efficient means for the wet-milling and micro-grinding of particles. Besides dispersing and deagglomerating, the wet milling is an important application of Hielscher ultrasonic devices.. In particular for the manufacturing of superfine-size slurries, ultrasound has many advantages, when compared with common size reduction equipment, such as: colloid
More