vrm cement grainding mill
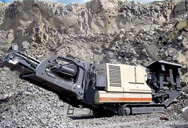
OK™ Raw and Cement Mill
Our best-in-class OK™ Mill is a globally successful vertical roller mill solution for grinding raw material, cement and slag. Its cutting-edge design features consistently deliver the highest quality products with the greatest efficiency. It
More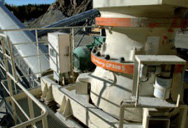
Cement mill - Wikipedia
A cement mill (or finish mill in North American usage [1]) ... have been used for cement grinding. The grinding action employs much greater stress on the material than in a ball mill, and is therefore more efficient. Energy consumption is typically half that of a ball mill. However, ...
More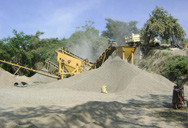
Vertical roller mills FLSmidth Cement
Whether grinding raw coal, clinker, cement and/or slag, we have a VRM solution to suit your grinding needs. What’s more, our online condition monitoring services enable you to adopt a proactive maintenance strategy for your OK™
More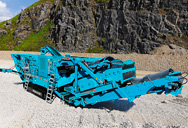
VRM – AMCL Machinery Limited
Construction of VRM. The mill consists of the lower casing, uppercasing, table mounted on the vertical planetary gear reducer, ... Over the years UBE has well-established 2+2 and 3+3 system of Main Roller and Sub Roller for Cement
More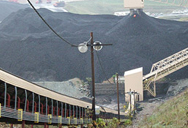
OK™ mill The most reliable and efficient mill for raw and cement grinding
Mill (VRM) designs for raw, fuel and cement grinding for several decades. The OK™ mill has been FLSmidth’s standard cement VRM since 1993. Since its introduction, the OK mill has proven to be the most efficient cement VRM available, with the highest reliability and ease of operation. In 2017,
More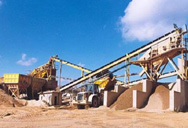
PROCESS CONTROL FOR CEMENT GRINDING IN VERTICAL ROLLER MILL (VRM
Optimization of cement grinding using standard bond grinding calculations based on population balance models is successfully applied [4, 38]. Various grinding laws, energy relationships, control factors and controller design for cement grinding are discussed in [37]. Figure-1. Vertical roller mill for cement grinding [13]. VRM shown in Figure-1 ...
More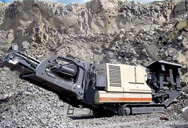
Cement Ball Mill Cost Effective Cement Grinding Mill from AGICO
The installation of liners. Length Diameter Ratio. The length-diameter ratio of the cement ball mill is relatively large. For mills of open-circuit grinding system, the length-diameter ratio is usually between 3.5 and 6 to ensure that the product fineness is qualified through single grinding; For ball mills in closed-circuit grind system, in order to increase the material flow rate, the length ...
More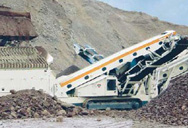
Cement grinding Vertical roller mills VS ball mills
However, a vertical roller mill for cement grinding generally requires the use of grinding aid to achieve the most efficient operation with a stable grinding bed and a low level of vibrations. ... The equipment footprint for a VRM is more compact than a ball mill; there is only a single foundation for the mill and one for the mill fan. Figure 9:
More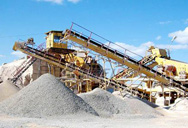
VRM In Cement Plant Maximize Energy Saving CNBM-SINOMA
Vertical roller mill manufacturers. Vertical roller mill or VRM is a large-scale grinding equipment designed for pulverizing cement raw meal, cement clinker, slag, coal, fly ash, limestone, and other hard grinding material.It integrates grinding, drying, separation, and conveying in one machine. The equipment is widely used in many industries such as cement, electric power,
More
Vertical roller mill vs. ball mill for cement grinding: Comparison
A Vertical Roller Mill (VRM) is an advanced and efficient grinding machine commonly used in the cement industry for grinding raw materials and clinker. VRMs have become increasingly popular due to their ability to produce finer products with lower energy consumption compared to traditional ball mills.
More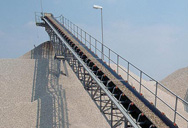
Cement grinding: VRM or ball mill?
2019年2月9日 Introduction Vertical roller mills (VRM) have become the standard for grinding raw materials in the cement manufacturing process. However, despite the fact that more than 10 years has passed since ...
More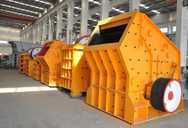
Cement Industry - Loesche
Our designers are constantly coming up with new ideas and even more dependable components to reduce the already acclaimed low failure rate of our mills. The roller grinding mill technology, patented in 1928 and continuously
More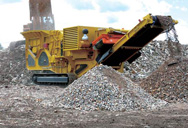
Everything you need to know about clinker/cement
For a cement mill: intermediate or outlet diaphragm. For the case of; cement mills with a drying chamber see raw mills. Mill working conditions: ventilation air speed through the mill. Bigger or smaller than 1.2 [m/s]. Material abrasivity.
More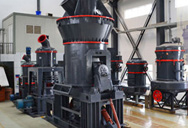
VRM – THE LATEST TECHNOLOGY - Bashundhara
Vertical Roller Mill (VRM) is the most advanced technology in cement production procedure. Bashundhara Cement has adopted VRM from LOESCHE, Germany in both the factories to ensure the best quality. With higher fineness achieved
More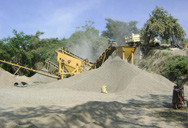
OPTIMIZATION OF CEMENT GRINDING OPERATION IN BALL MILLS
Condition in one of the grinding chambers of the mill . Results of Optimization . The graphical analysis presented in Figure 2 represents progress of grinding along the length of the mill after optimizing the grinding process. rogress of grinding is clearly visible in Desired p the graphs. Figure -2: Analysis of longitudinal samples.
More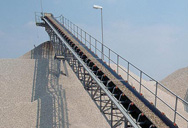
2 µm 5 µm - Loesche
1985 Mills for grinding cement and granulated blast furnace slag were installed in Asia under licence from Loesche. 1994 The 2+2 technology, which was specially developed for grinding clinker and granulated blast furnace slag, was used for the first time in an LM 46.2+2 for cement grinding in the Pu Shin mill works of Lucky Cement, Taiwan.
More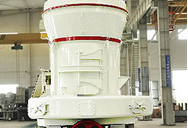
Review on vertical roller mill in cement industry its performance ...
2021年1月1日 As per European cement research academy's project “Future grinding technologies”, out of 1036 orders of grinding mills in 5 years, 58% were for Vertical Roller mill and 40% were for Ball Mill + HPGR circuit. Hence Ball Mill VRM are major technologies in cement grinding. Their technological comparison is done beneath [8].
More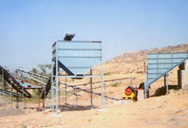
polysius® booster mill
A grinding plant – including the agitated bead mill, a ball mill, HPGR, combi grinding and VRM - and laboratories within thyssenkrupp RD center enable offering of polysius ® lab services. Here the adaptation and optimization of binder properties by physical, chemical and mineralogical analysis as well as mortar testing are carried on customer’s behalf.
More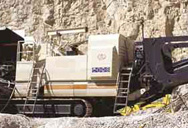
Improvements in New Existing Cement Grinding Mills by Tim
o Finished grinding may consume 25 – 50 kWh/t cement, depending on the feed material grindability, additives used, plant design especially the required cement fineness. Cement grinding is the single biggest consumer of electricity in the manufacturing process. Whichever the mill types, grinding is inherently inefficient
More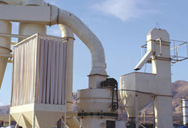
Comparing ball mills and VRMS for cement grinding
2013年2月26日 This is an abridgedversion of the full article, which appeared in the March 2013 issue of World Cement. Subscribers can view the full article by logging in. Introduction. Vertical roller mills (VRM) have become the standard for grinding raw materials in the cement manufacturing process.
More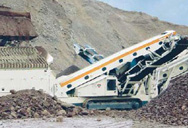
The cement mill
Cement manufacturing - brief description of a cement mill. Cement clinker is usually ground using a ball mill. This is essentially a large rotating drum containing grinding media - normally steel balls. As the drum rotates, the motion of the balls crushes the clinker. The drum rotates approximately once every couple of seconds.
More