dyestuffs ball milling process
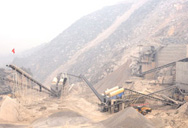
Ball milling: a green technology for the preparation and ...
Ball milling is a simple, fast, cost-effective green technology with enormous potential. One of the most interesting applications of this technology in the field of cellulose is the preparation
More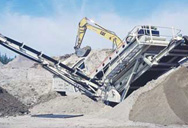
Research progress on synthesis mechanism and performance
2024年6月3日 This article presents an overview of the fundamental principles underlying ball milling technology, encompassing aspects such as ball milling pre-treatment, biochar
More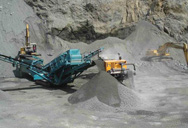
Ball milling: a green technology for the preparation and ...
Ball milling is a simple, fast, cost-effective green technology with enormous potential. One of the most interesting applications of this technology in the
More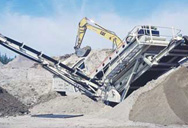
Recent Advances in Ball-Milled Materials and Their
2024年6月7日 A ball milling process is realized by a ball grinding mill machine. The working method is to put precursors and grinding mediums into a ball mill container and set operating parameters. Because ball milling is a
More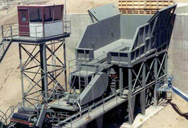
Materials Development Using High-Energy Ball Milling:
2022年6月17日 High-energy ball milling (HEBM) of powders is a complex process involving mixing, morphology changes, generation and evolution of defects of the crystalline lattice, and formation of new phases.
More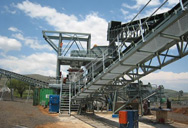
Ball Milling Towards Green Synthesis: Applications, Projects ...
2014年11月26日 Ball milling has emerged as a powerful tool over the past few years for effecting chemical reactions by mechanical energy. Allowing a variety of reactions to occur at
More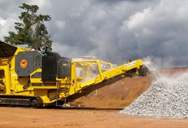
Process Control of Ball Mill Based on MPC-DO - Wiley Online Library
Furthermore, a compound control strategy for process control of the ball mill is proposed to describe the grinding process precisely where disturbances exist. It consists of two types of
More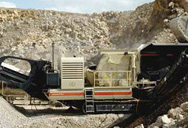
“Ball Milling Towards Green Synthesis: Applications, Projects ...
By By Daniel Sheldon. Lithium Recovery from Aqueous Resources and Batteries: A Brief Review. Authors: Ling Li, Vishwanath G. Deshmane, M. Parans Paranthaman, Ramesh Bhave, Bruce
More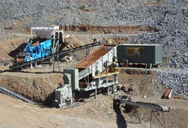
Ball milling as an important pretreatment technique in
2021年8月12日 The multi-step milling process uses preliminary milling before ball milling to reduce the lignocellulosic biomass particle size from coarse to a fine powder. This sequential
More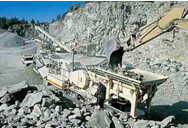
Effect of Ball-Milling Process on Microstructures and Mechanical ...
2022年6月23日 In this work, several heterogeneity-improved heterostructured 2024Al alloys by introducing in-situ Al3Ti particles were prepared by using powder thixoforging (PTF) with different high-energy ball-milling methods, and the microstructures and mechanical properties of the resultant alloys were investigated. The results indicate that all the alloys have a
More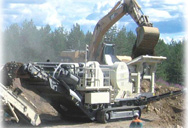
Ball milling: a green technology for the preparation
The use of ball milling as a defibrillation method after a series of pre-treatments of raw materials was also described by the group of Elkoun, who reported the extraction of CNFs and CNCs from carrot pulp by ball milling and acid
More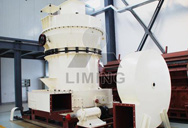
The use of pomegranate seed activated by mechanochemical process
2020年6月10日 Abstract This study aims to reveal the potential of using pomegranate seed (PS) as an alternative, new and cost-effective adsorbent for the removal of anionic dyestuffs such as Congo Red (CR) and Remazol Brillant Blue R (RBBR) from aqueous solutions. In addition, the PS was activated by a high-energy planetary ball milling. It was seen that the activated PS (APS)
More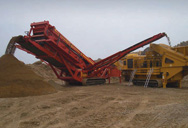
Comparative Study on Improving the Ball Mill Process Parameters ...
2021年2月19日 For ball mill working capacity, the optimum process parameter level No.3 (2.0 L) with a value of SN ratio (-12.915) based on smaller-the-better characteristic while for ball milling speed level No.2 (105 RPM) with a value of SN ratio as (-13.386) based on smaller-the-better characteristic, is the optimum process parameter level.
More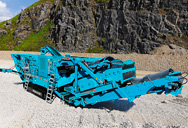
Ball-milling – Nanoscience and Nanotechnology I - INFLIBNET
The ball milling process can be summed up as: a. It consists of stainless steel chamber and several small iron, silicon carbide, hardened steel, or tungsten carbide balls to rotate inside the mill. b. Powder of material is put in the steel chamber.
More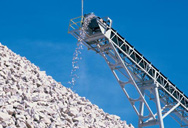
Advance in chatter detection in ball end milling process by
2013年7月4日 This paper presents an advance in chatter detection in ball end milling process. The dynamic cutting forces are monitored by utilizing the wavelet transform. The new three parameters are introduced to classify the chatter and the non-chatter by taking the ratio of the average variances of dynamic cutting forces to the absolute variances of themselves. The
More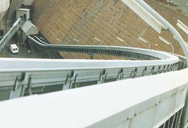
Prediction of surface roughness in ball-end milling process by ...
2014年8月20日 The aim of this research is to propose the practical model to predict the in-process surface roughness during the ball-end milling process by utilizing the dynamic cutting force ratio. The proposed model is developed based on the experimentally obtained results by employing the exponential function with five factors of the spindle speed, the feed rate, the tool
More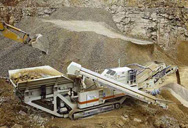
Planetary Ball Mill Process in Aspect of Milling Energy - Powder
Introduction Milling is a core fabrication process in powder technology. Especially the high-energy milling technology is being frequently used in energy-intensive process like mechanical alloying, mechanical activation and mechanochemistry, etc. Planetary ball mill is a representative highenergy mill together with shaker mill, stirred mill and vibration mill.
More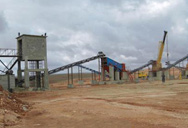
Materials Development Using High-Energy Ball Milling: A Review
2022年6月17日 High-energy ball milling (HEBM) of powders is a complex process involving mixing, morphology changes, generation and evolution of defects of the crystalline lattice, and formation of new phases. This review is dedicated to the memory of our colleague, Prof. Michail A. Korchagin (1946–2021), and aims to highlight his works on the synthesis of materials by
More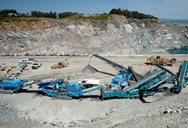
Ball Mill PPT - SlideShare
2015年11月30日 If the rate of feed increased, coarser product will be obtained and if speed of rotation is increased the fineness for a given capacity is increases. During grinding, the balls themselves wear and are continuously replaced by new ones so that mill contains balls of various ages. Ball mill produces 1 to 50 ton/hr of powder and energy requirement of the ball mill is
More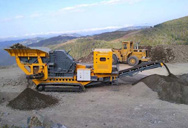
The effect of mechanical activation duration on the structure and ...
2023年6月1日 TiO 2 is popular in modern industries, including dyestuffs, printing, and cosmetics. To convert titanium slag to TiO 2 with maximum efficiency, mechanical activation is an important pretreatment step to control the particle size of the titanium slag and the subsequent leaching process. Our study used a planetary high-energy ball mill to wet the titanium slag by
More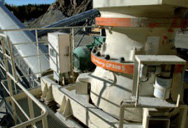
High-temperature ball milling: An efficient method to fabricate Ti
2024年3月1日 To match the actual ball milling process, a nonlinear elastic Hertz–Mindlin no-slip contact model [31] relying on the viscous damping effect for energy dissipation [32] was adopted in this study. Download: Download high-res image (170KB) Download: Download full
More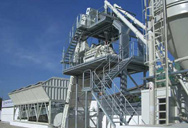
Process intensification effect of ball milling on the hydrothermal ...
2015年9月1日 Enhancement of the cellulose accessibility is significant for biomass enzymatic hydrolysis. Here, we reported an efficient combined pretreatment for corn straw enzymolysis using ball milling and dilute acid hydrothermal method (a mixture solvent of H 2 O/ethanol/sulfuric acid/hydrogen peroxide liquid). The process intensification effect of ball
More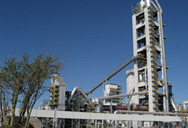
Ball milling grinding PPT Free Download - SlideShare
2021年4月24日 14. High ball milling: Ball milling process where a powder mixture placed in the ball mill is subjected to high-energy collision from the balls. This process was developed by Benjamin and his coworkers at the International Nickel Company in the late of 1960. It was found that this method, termed mechanical alloying, could successfully produce fine, uniform
More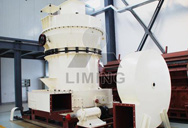
The use of pomegranate seed activated by mechanochemical process
2020年6月10日 Abstract This study aims to reveal the potential of using pomegranate seed (PS) as an alternative, new and cost-effective adsorbent for the removal of anionic dyestuffs such as Congo Red (CR) and Remazol Brillant Blue R (RBBR) from aqueous solutions. In addition, the PS was activated by a high-energy planetary ball milling. It was seen that the activated PS (APS)
More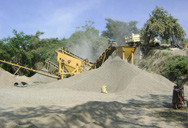
What Are Different Techniques to Synthesis Nanomaterial? Explain
BALL MILLING PROCESS : 1. 1. As the name suggests, the ball milling method consists of balls and a mill chamber. Therefore over all a ball mill contains a stainless steel container and many small iron, hardened steel, silicon carbide, or tungsten carbide balls are made to rotate inside a mill (drum). 2.
More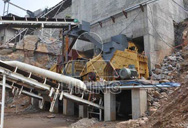
The ball milling parameters for different samples (PCA: process
The ball milling process can be both dry and wet depending on the necessity: in wet ball milling, a solution is added as PCA to reducing the maximum temperature reached during the process [101].
More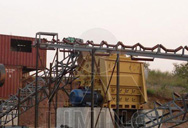
Ball milling process variables optimization for high-entropy alloy ...
2023年9月1日 In what follows, considering the milling time required to develop single-phase solid-solution HEA, finest particle- and grain- sizes, ethanol PCA (wet milling) shows to be more effective than the stearic acid PCA (dry milling) for MA of AlCoCrFe HEA; hence, milling speed, milling time, and the amount of ethanol PCA will be considered as input parameters/process
More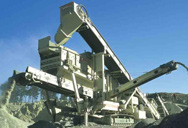
US4859770A - Process for making alpha-phase ... - Google Patents
U.S. Pat. No. 4,257,951 (the '951 patent) discloses a two-step milling process for preparing pigmentary copper phthalocyanine. The milling process utilizes both an aluminum salt and an organic solvent in both the first grinding step and the second grinding step, followed by treating the milled product with an organic liquid in water emulsion.
More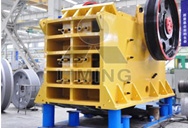
Regularity and mechanism of wheat straw properties change in ball
2017年10月1日 CK was ball milled using a CJM-SY-B vibration ball milling (Qinhuangdao Taiji Ring Nano Ltd., Hebei, China) with circulating cooling system to maintain the milling process below 30 °C. CK and zirconia beads (6–10 mm diameter) were mixed in a 2 L Zirconia tank with filling ratio of milling ball 35% and ball to sample ratio 2:1, milling for 0.5, 1.0, 1.5, 2.0, 4.0,
More